В начале августа 2016
года ВМС США осуществили успешные испытания конвертоплана Osprey MV-22.
Сам по себе этот летательный аппарат не является чем-то необычным.
Двухвинтовая машина достаточно давно находится на вооружении
американского флота (она была принята на вооружение во второй половине
1980-х годов), однако впервые в истории на конвертоплане были
установлены критически важные детали (от них напрямую зависит
безопасность полета), которые были напечатаны на 3D-принтере.
Для
проведения испытаний американские военные напечатали из титана методом
прямого послойного лазерного спекания кронштейн крепления двигателя к
крылу конвертоплана. При этом на сам кронштейн был смонтирован
тензодатчик, предназначенный для регистрации возможной деформации
детали. Каждый из двух двигателей конвертоплана Osprey MV-22 крепится к
крылу с помощью четырех таких кронштейнов. При этом на момент первого
испытательного полета конвертоплана, который состоялся 1 августа 2016
года, на нем был установлен всего один напечатанный на 3D-принтере
кронштейн. Ранее уже сообщалось, что на конвертоплан также были
установлены напечатанные методом трехмерной печати крепления мотогондол.
Разработкой
напечатанных для конвертоплана деталей занимался Центр боевого
применения авиации ВМС США, расположенный на объединенной базе
«Макгуайр-Дикс-Лейкхерст» в Нью-Джерси. Летные испытания Osprey MV-22 с
напечатанными на принтере деталями прошли на базе ВМС США
«Патксент-Ривер», испытания были признаны военными полностью успешными.
Американские военные считают, что благодаря широкому внедрению
трехмерной печати техники в будущем смогут достаточно быстро и
сравнительно дешево изготавливать запасные части для конвертопланов. При
этом нужные детали можно будет печатать непосредственно на кораблях.
Помимо этого, отпечатанные детали можно будет затем модифицировать для
того, чтобы улучшить характеристики бортовых агрегатов и систем.
Напечатанный из титана кронштейн крепления двигателя
Американские
военные были заинтересованы в технологиях трехмерной печати еще
несколько лет назад, но до недавних пор функционал 3D-принтеров был не
настолько широк, чтобы его можно было использовать в обыденном режиме
для построения достаточно сложных деталей. Детали для конвертоплана были
созданы с помощью 3D-принтера аддитивной печати. Деталь изготавливается
постепенно слоями. Каждые три слоя титановой пыли скрепляются лазером,
этот процесс повторяется столько, сколько нужно, чтобы получилась
необходимая форма. После завершения лишнее с детали срезается;
полученный элемент полностью готов к использованию. Так как испытания
завершились успешно, американские военные не будут останавливаться на
достигнутом, они собираются построить еще 6 важных элементов конструкции
конвертоплана, половина из которых также будет титановой, а другая —
стальной.
Трехмерная печать в России и мире
Несмотря
на то, что принтерный вид производства был успешно реализован в США и
России несколько лет назад, создание элементов для военной техники
находится в процессе доработки и испытаний. Прежде всего это связано с
очень высокими требованиями, предъявляемыми ко всей военной продукции,
главным образом, по надежности и прочности. Тем не менее, успеха в этой
области добились не одни лишь американцы. Российские конструкторы уже
второй год производят детали для разрабатываемых автоматов и пистолетов с
помощью технологии трехмерной печати. Новые технологии позволяют
экономить драгоценное время на чертежах. А постановка подобных деталей
на поток может обеспечить быструю замену на местах, в ремонтных
батальонах, так как исчезнет необходимость ждать поступления запчастей с
завода для тех же танков или беспилотных летательных аппаратов.
Для
подводников военные 3D-принтеры будут просто на вес золота, так как при
автономном дальнем плавании замена деталей силами самих подводников
даст подлодке практически неисчерпаемый ресурс. Схожая ситуация
наблюдается и с кораблями, отправляющимися в дальнее плавание,
ледоколами. Большинство таких кораблей в самое ближайшее время получит
беспилотники, которые со временем потребуют ремонта или полной замены.
Если на корабле появится 3D-принтер, который позволит оперативно
печатать запасные части, то через несколько часов технику можно будет
использовать вновь. В условиях скоротечности операций и высокой
мобильности театра военных действий локальная сборка тех или иных
деталей, узлов и механизмов прямо на месте позволит сохранить высокий
уровень эффективности частей обеспечения.
Osprey MV-22
Пока
в США военные запускают свои конвертопланы, российские производители
танка «Армата» уже второй год пользуются на «Уралвагонзаводе»
промышленным принтером. С его помощью выпускаются детали для
бронетехники, а также продукции гражданского назначения. Но пока что
такие детали используются лишь для прототипов, к примеру, они
использовались при создании танка «Армата» и его испытаниях. В концерне
«Калашников», а также в «ЦНИИТОЧМАШ» по заказу российских военных
конструкторы делают разнообразные части стрелкового оружия из
металлической и полимерной крошки на 3D-принтерах. Не отстает от них и
тульское Конструкторское бюро приборостроения имени Шипунова, знаменитое
КПБ, которое известно богатым ассортиментом выпускаемого оружия: от
пистолетов до высокоточных ракет. К примеру, перспективный пистолет и
автомат АДС, который призван заменить у бойцов спецподразделений АК74М и
АПС, собирается из деталей из высокопрочного пластика, которые
печатаются на принтере. Под некоторые военные изделия в КПБ уже смогли
создать пресс-формы, в настоящее время прорабатывается серийная сборка
изделий.
В условиях, когда в мире наблюдается новая гонка
вооружений, становятся важны сроки выпуска новых образцов оружия. К
примеру, в бронетехнике лишь процесс создания макета и перенос с
чертежей на прототип занимает обычно год-два времени. При разработке
подводных лодок этот срок уже в 2 раза больше. «Технология трехмерной
печати позволит сократить сроки в разы до нескольких месяцев, — отмечает
эксперт в области военно-морского флота Алексей Кондратьев. —
Конструкторы смогут сэкономить время на чертежах при проектировании на
компьютере 3D-модели и сразу изготовить прототип нужной детали. Очень
часто детали переделываются с учетом проведенных испытаний и в процессе
доработки. При этом можно выпустить сборку вместо детали и проверить все
механические характеристики, как взаимодействуют части между собой. В
конечном итоге сроки создания прототипа позволят конструкторам уменьшить
общий срок выхода первого готового образца на стадию испытаний. В наши
дни для создания атомной субмарины нового поколения требуется порядка
15-20 лет времени: от эскиза до последнего винта при сборке. При
дальнейшем развитии промышленной трехмерной печати и выходе на серийное
производство деталей таким способом сроки можно будет уменьшить минимум в
1,5-2 раза».
Согласно оценкам экспертов, современные технологии
находятся сегодня в одном-двух годах от массового производства на
3D-принтерах титановых деталей. Можно с уверенностью говорить о том, что
до конца 2020 года военные представители на предприятиях
оборонно-промышленного комплекса будут принимать технику, которая на
30-50% будет собрана при помощи технологий трехмерной печати. При этом
наибольшее значение для ученых представляет создание на 3D-принтере
керамических деталей, которые отличаются высокой прочностью, легкостью и
теплозащитными свойствами. Данный материал очень широко используется в
космической и авиационной отрасли, но может применяться в еще больших
объемах. К примеру, создание на 3D-принтере керамического двигателя
открывает горизонты для создания гиперзвуковых самолетов. Обладая таким
двигателем, пассажирский самолет мог бы долететь из Владивостока до
Берлина за пару часов.
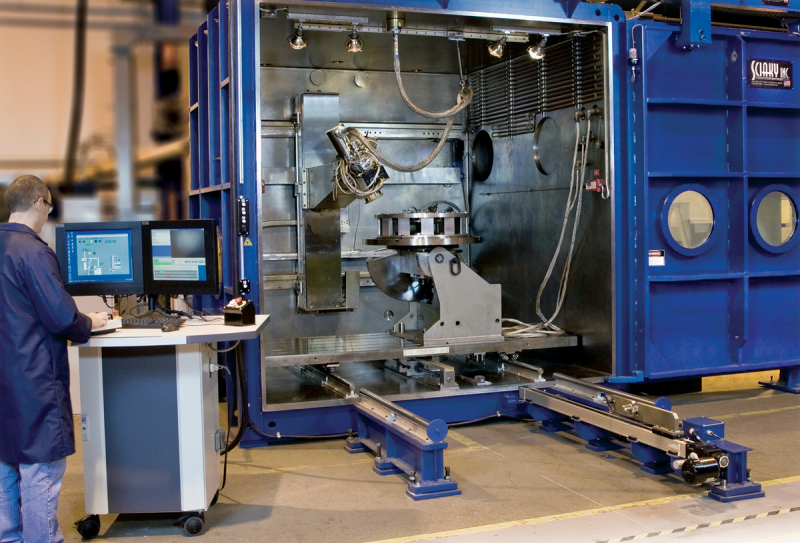
Также
сообщается, что американские ученые изобрели формулу смолы специально
для печати в 3D-принтерах. Ценность данной формулы — в высокой прочности
получаемых из нее материалов. К примеру, подобный материал может
выдерживать критические температуры, которые превышают 1700 градусов
Цельсия, это в десятки раз выше устойчивости многих современных
материалов. По оценкам Стефани Томпкинс, занимающей пост директора
научного управления в передовых оборонных исследованиях, новые
материалы, создаваемые на 3D-принтерах, будут обладать уникальными
сочетаниями характеристик и свойствами, до этого еще не
использовавшимися. По словам Томпкинс, благодаря новым технологиям мы
сможем получить прочную деталь, обладающую маленькой массой и огромными
размерами. Ученые полагают, что производство деталей из керамики на
3D-принтере будет означать научный прорыв, в том числе в производстве
продукции гражданского назначения.
Первый российский 3D-спутник
В
настоящее время с помощью технологии трехмерной печати уже успешно
выпускаются детали прямо на борту космических станций. Но отечественные
специалисты решили пойти еще дальше, они сразу решили создать с помощью
3D-принтера микроспутник. Ракетно-космическая корпорация «Энергия»
создала спутник, корпус, кронштейн и ряд других деталей которого были
распечатаны на 3D-принтере. При этом важное уточнение состоит в том, что
микроспутник был создан инженерами «Энергии» совместно со студентами
Томского политехнического университета (ТПУ). Первый принтерный спутник
получил полное название «Томск-ТПУ-120» (цифра 120 в названии в честь
120-летия вуза, которое отмечалось в мае 2016 года). Он был успешно
запущен в космос весной 2016 года вместе с космическим кораблем
«Прогресс МС-02», спутник был доставлен на МКС и затем выведен в космос.
Данный аппарат является первым и единственным в мире 3D-спутником.
Спутник,
созданный студентами ТПУ, относят к классу наноспутников (CubSat). Он
имеет следующие размеры 300х100х100 мм. Данный спутник стал первым в
мире космическим аппаратом, корпус которого был напечатан с помощью
технологии трехмерной печати. В будущем данная технология может стать
настоящим прорывом в создании небольших спутников, а также сделает их
использование более доступным и массовым. Конструкция космического
аппарата была разработана в научно-образовательном центре «Современные
производственные технологии» ТПУ. Материалы, из которых был произведен
спутник, были созданы учеными Томского политехнического университета и
Института физики прочности и материаловедения СО РАН. Основной целью
создания спутника было испытание новых технологий космического
материаловедения, он поможет российским ученым протестировать несколько
разработок томского вуза и его партнеров.
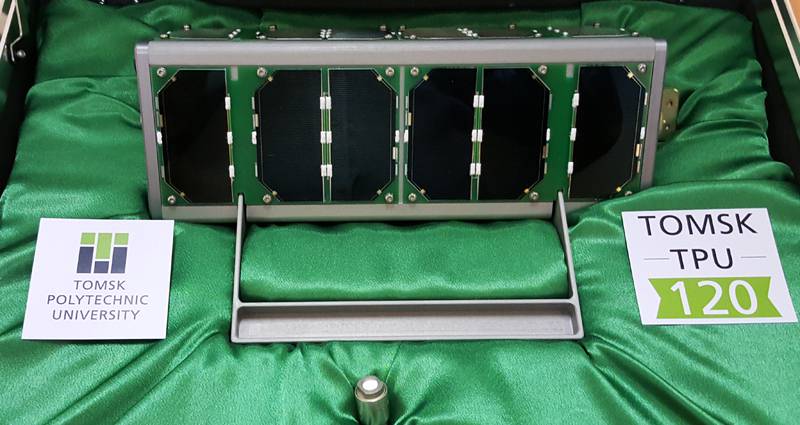
По
информации пресс-службы вуза, запуск наноспутника «Томск-ТПУ-120»
планировалось осуществить во время выхода космонавтов с МКС в открытый
космос. Спутник представляет собой достаточно компактный, но в то же
время полноценный космический аппарат, обладающий элементами питания,
солнечными батареями, бортовой радиоаппаратурой и другими приборами. Но
главной его особенностью было то, что его корпус был напечатан на
3D-принтере.
Разные датчики наноспутника будут фиксировать
температуру на борту, на батареях и платах, параметры электронных
компонентов. Вся эта информация будут передаваться затем на Землю в
режиме онлайн. По этой информации российские ученые смогут анализировать
состояние материалов спутника и решать, будут ли они использовать их
при разработке и строительстве космических аппаратов в дальнейшем. Стоит
отметить, что немаловажным аспектом разработки малых космических
аппаратов является также и подготовка новых кадров для отрасли. Сегодня
студенты и преподаватели Томского политеха собственными руками
разрабатывают, производят и усовершенствуют конструкции всевозможных
малых космических аппаратов, получая при этом не только качественные
фундаментальные знания, но также и необходимые навыки практической
работы. Именно это в дальнейшем и делает выпускников данного учебного
заведения уникальными специалистами.
В дальнейших планах
российских ученых и представителей промышленности — создание целого
«роя» университетских спутников. «Мы говорим сегодня о том, что
необходимо мотивировать наших студентов на изучение всего, что, так или
иначе, связано с космосом — это могут быть и энергетика, и материалы, и
создание двигателей нового поколения и т.д. Мы обсуждали ранее, что
интерес к космосу в стране несколько угас, однако его можно возродить.
Для этого необходимо начинать даже не со студенческой скамьи, а еще со
школьной. Таким образом, мы и вышли на путь разработки и выпуска CubeSat
— небольших спутников», — отмечает пресс-служба Томского политеха со
ссылкой на ректора данного высшего учебного заведения Петра Чубика.
Источники информации:
//www.utro.ru/articles/2016/08/15/1293813.shtml
https://nplus1.ru/news/2016/08/04/video
//news.tpu.ru/news/2016/02/02/24769
//ria.ru/space/20160401/1400943777.html